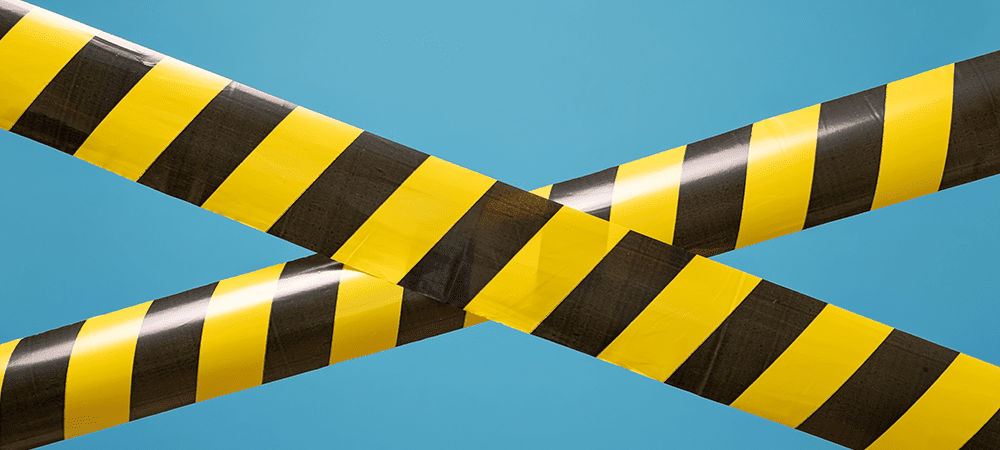
Understanding Safety Hazards Within the Workplace
Last modified on March 20th, 2025
How to Identify and Reduce Common Safety Hazards Within the Workplace
You should always be on the lookout for safety hazards in the workplace. While it’s difficult to fully and completely guard against every potential risk, identifying common workplace hazards can help you put together a good plan to keep all of your employees as safe as possible.
It’s important to have the right information on hand to ensure you’re able to spot safety hazards before they cause harm to any of your employees. Continue reading to learn more about the most common workplace hazards and how to put the right plan together to guard against them.
6 Common Workplace Safety Hazard Types and Examples
Workplace safety hazards come in many different forms. While some might be a little more obvious, others can be a bit tricky to pinpoint. Here are the main types of safety hazards you should be aware of:
- General workplace safety hazards: These include any risk likely to cause falls, slips or trips and lead to injury, illness or even death. They’re most common on construction sites or other settings where employees must operate machinery.
- Biological hazards: Biohazards involve any materials or substances that could have a harmful effect on human health. While this often includes infection from viruses, it can also mean contact with bodily fluids, blood, fungus, medical waste, insects and a number of nasty toxins. Healthcare, agriculture and laboratory workers face the highest risks of biological hazards, but any industry dealing with hazardous materials should implement strict hazard communication and protective measures.
- Physical hazards: These pose a danger to the physical safety and well-being of your employees. They are more commonly associated with physically demanding jobs (like overexposure to sun or cold outdoor conditions), but physical hazards can affect any workplace. Noise and overly confined workspaces can also pose physical safety risks. Occupational safety programs should address these risks through proper ventilation, noise reduction strategies and protective gear.
- Ergonomic hazards: Think body strain. Work environments that encourage employees to contort their bodies can lead to serious injury. This usually includes repetitive motion, lifting, pushing or pulling heavy objects, but even in office settings, spending too much time hunched over a laptop is associated with a range of ill health effects. When it comes to office ergonomics, it’s important to know how to protect your workers.
- Chemical hazards: It’s no secret that exposure to certain chemicals can cause serious harm. Dangerous substances can come in many different forms, including gases, liquids and solids, so they can sometimes be tough to detect with the naked eye. Workers in construction, manufacturing and cleaning services must follow strict safety protocols for handling chemical hazards and refer to safety data sheets for proper storage and use. Potential hazards include anything from skin irritants and carcinogens to chemical fires and corrosion. Workplace hazard communications prevent employee exposure to dangerous chemical products.
- Psychological hazards: Often overlooked, psychological hazards affect mental well-being. Workplace violence, bullying, stress and long hours contribute to occupational hazards that lead to burnout and decreased productivity. Common psychological hazards include overstress and fatigue, while the more serious risks involve bullying and even physical violence.
By recognizing and addressing these common hazards, your business can create a safer environment for employees and reduce workplace injuries. Implementing preventive measures and fostering a strong safety culture ensures long-term workplace safety and compliance with occupational safety regulations.
How Do You Know if Safety Hazards are Present in Your Workplace?
Understanding hazards within the workplace is essential but identifying whether they actively pose a risk to employees requires a keen eye and thorough assessment.
Some workplace hazards are visible, such as electrical hazards or trip hazards, while others, like psychosocial hazards, may be harder to detect. Employers must stay proactive in identifying potential risks before they lead to workplace injuries or violations of occupational safety standards.
To determine whether safety hazards exist in your workplace, ask these key questions:
- Are employees frequently injured, or are they reporting an issue that’s making them concerned about their safety?
- How often are problems arising?
- Where in your workplace are the most common issues happening?
- What conditions have workers brought to your attention?
How to Conduct a Safety Assessment to Identify and Correct Hazards
OK, so you’ve gathered enough information from your employees to determine that there are hazards in your workplace – now it’s time to identify them and put a course of action in place to address and correct them. Every good game plan starts by targeting the main culprits, so you should assess all past injuries, illnesses and other incidents to narrow in on the most serious hazards.
Identifying workplace hazards:
- Safety suggestion program: Establish an anonymous hazard reporting system where employees can share concerns about workplace safety hazards. Employees will feel like their opinions are valued, encouraging them to make more suggestions, and you’ll get a raft of useful information to help guide your decisions. It’s a win-win for everybody.
- Safety committee: A designated committee provides a more formal opportunity for all members of your organization to come together and discuss safety hazards in the workplace. Set up an effective safety committee tasked with investigating accidents, taking corrective action and devising safety programs.
- Safety meeting participation: Ask your employees to attend and participate in regular safety meetings. You can encourage more meaningful participation by asking employees to share their own workplace experiences and offer suggestions for how to prevent similar incidents from happening again.
- Workplace evaluation: The best plans are those that are constantly evaluated and updated to account for the latest hazards. Take a quick daily look through all work areas. This can be enough to prevent major problems down the road.
OSHA Regulations to Consider
Always consider the following regulations put in place by the Occupational Safety and Healthcare Administration (OSHA) as they relate to your practice:
Workplace Hazard | OSHA Standard |
Working with chemicals | Hazard Communication Standard |
Working in confined spaces | Confined Spaces Standard |
Loud noise in the workplace | Hearing Conservation Standard |
Chemical spills | Emergency Response Standard |
Fire | Emergency Action & Fire Prevention Standard |
Hazards of machinery | Machine Guarding Standard |
Falling from heights | Fall Protection Standard |
Hazards of energy sources | Lock Out/Tag Out Standard |
OSHA’s General Duty Clause outlines what employers should do to protect employees from workplace hazards.
Preparing for the Future
Health and safety always come first, but sometimes the unexpected happens. Workers’ compensation insurance is the best way to safeguard the wellness of your employees and keep your company up and running. FFVA Mutual is here to help. Do you have questions about workplace hazards, OSHA training, safety programs, drug-free workplace, fleet safety, return to work or other safety-related challenges? Simply ask a safety question and one of our expert safety consultants will get back to you with an answer!
FROM OUR BLOG
SEE MORE POSTS
How To Conduct a Safety Audit: A Step-by-Step Guide
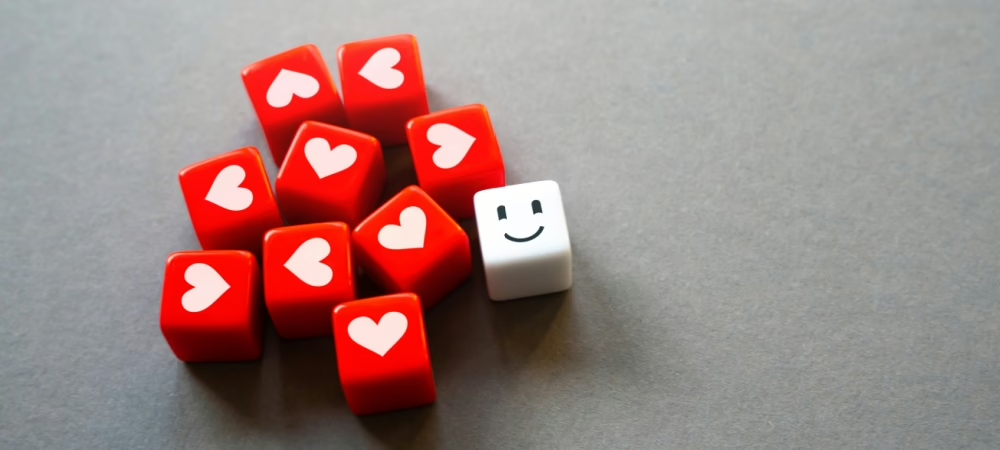
Behavior Based Safety: Your Guide to a Safer Workplace
![OSHA’s Most Frequently Cited Standards [infographic]](https://b1451152.smushcdn.com/1451152/wp-content/uploads/1000-x-450-for-blog-post-main-banner-1.png?lossy=1&strip=0&webp=1)